Die Vorteile von Magnesia-Kohlenstoffsteinen sind:Beständigkeit gegen Schlackenerosion und gute Temperaturwechselbeständigkeit.Der Nachteil von MgO-Cr2O3-Steinen und Dolomitsteinen bestand in der Vergangenheit darin, dass sie Schlackenbestandteile aufnahmen, wodurch es zu Strukturabplatzungen und damit zu vorzeitigen Schäden kam.Durch die Zugabe von Graphit beseitigten Magnesia-Kohlenstoffsteine diesen Mangel.Sein Merkmal ist, dass die Schlacke nur in die Arbeitsfläche eindringt, so dass die Reaktionsschicht auf die Arbeitsfläche beschränkt ist, die Struktur weniger abblättert und eine lange Lebensdauer hat.
Zusätzlich zu herkömmlichen Asphalt- und harzgebundenen Magnesia-Kohlenstoffsteinen (einschließlich gebrannter, ölimprägnierter Magnesia-Steine)Zu den auf dem Markt verkauften Magnesia-Kohlenstoffsteinen gehören::
(1) Magnesia-Kohlenstoffsteine aus Magnesia mit 96 % bis 97 % MgO und Graphit 94 % bis 95 % C;
(2) Magnesia-Kohlenstoffsteine aus Magnesia mit 97,5 % bis 98,5 % MgO und Graphit mit 96 % bis 97 % C;
(3) Magnesia-Kohlenstoffsteine aus Magnesia mit 98,5 % bis 99 % MgO und 98 % ~C-Graphit.
Je nach Kohlenstoffgehalt werden Magnesia-Kohlenstoffsteine eingeteilt in:
(I) Gebrannte, ölimprägnierte Magnesiasteine (Kohlenstoffgehalt unter 2 %);
(2) Kohlenstoffgebundene Magnesiasteine (Kohlenstoffgehalt weniger als 7 %);
(3) Kunstharzgebundener Magnesia-Kohlenstoffstein (Kohlenstoffgehalt beträgt 8 % bis 20 %, in einigen Fällen bis zu 25 %).Asphalt/harzgebundenen Magnesia-Kohlenstoffsteinen (Kohlenstoffgehalt beträgt 8 % bis 20 %) werden häufig Antioxidantien zugesetzt.
Magnesia-Kohlenstoffsteine werden durch die Kombination von hochreinem MgO-Sand mit schuppigem Graphit, Ruß usw. hergestellt. Der Herstellungsprozess umfasst die folgenden Prozesse: Zerkleinern des Rohmaterials, Sieben, Sortieren, Mischen entsprechend der Materialformel, dem Design und der Produkteinstellungsleistung Die Kombination Die Temperatur des Wirkstofftyps wird auf nahezu 100 bis 200 ° C erhöht und zusammen mit dem Bindemittel geknetet, um den sogenannten MgO-C-Schlamm (Grünkörpermischung) zu erhalten.Das MgO-C-Schlammmaterial aus Kunstharz (hauptsächlich Phenolharz) wird im kalten Zustand geformt;Das MgO-C-Schlammmaterial wird in Kombination mit Asphalt (in einen flüssigen Zustand erhitzt) in heißem Zustand (bei etwa 100 °C) geformt.Je nach Chargengröße und Leistungsanforderungen von MgO-C-Produkten können Vakuumvibrationsgeräte, Formpressgeräte, Extruder, isostatische Pressen, Heißpressen, Heizgeräte und Stampfgeräte zur Verarbeitung von MgO-C-Schlammmaterialien verwendet werden.zur idealen Form.Der geformte MgO-C-Körper wird zur Wärmebehandlung in einen Ofen bei 700–1200 °C gegeben, um das Bindemittel in Kohlenstoff umzuwandeln (dieser Prozess wird Karbonisierung genannt).Um die Dichte von Magnesia-Carbon-Steinen zu erhöhen und den Verbund zu stärken, können zur Imprägnierung der Steine auch bindemittelähnliche Füllstoffe eingesetzt werden.
Als Bindemittel für Magnesia-Carbon-Steine wird heutzutage meist Kunstharz (insbesondere Phenolharz) verwendet.Der Einsatz von kunstharzgebundenen Magnesia-Carbonsteinen hat folgende grundsätzliche Vorteile:
(1) Umweltaspekte ermöglichen die Verarbeitung und Herstellung dieser Produkte;
(2) Der Prozess der Herstellung von Produkten unter Kaltmischbedingungen spart Energie;
(3) Das Produkt kann unter nicht aushärtenden Bedingungen verarbeitet werden;
(4) Im Vergleich zum Teer-Asphalt-Bindemittel gibt es keine plastische Phase;
(5) Ein erhöhter Kohlenstoffgehalt (mehr Graphit oder Steinkohle) kann die Verschleißfestigkeit und Schlackenbeständigkeit verbessern.
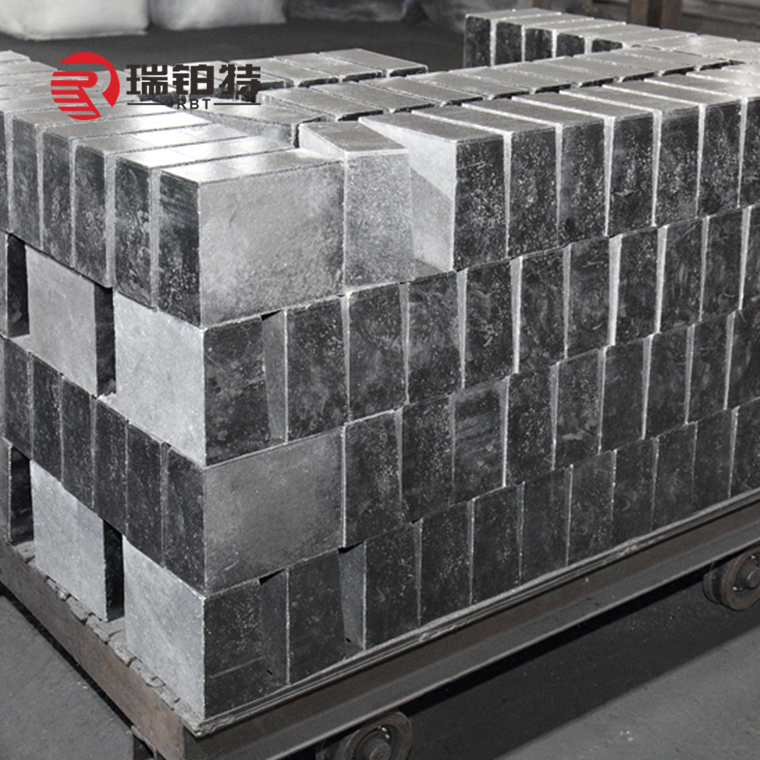
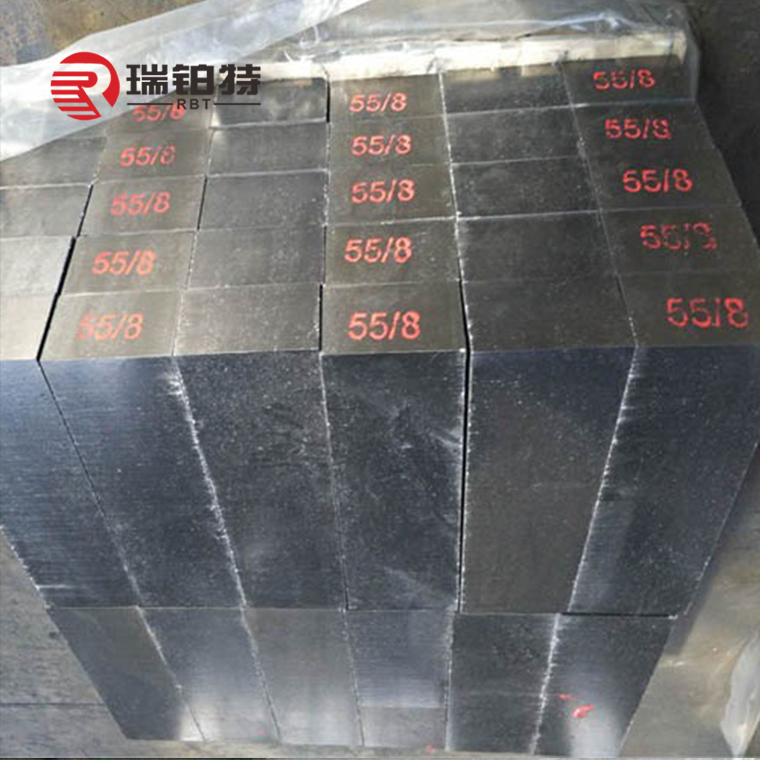
Zeitpunkt der Veröffentlichung: 23. Februar 2024