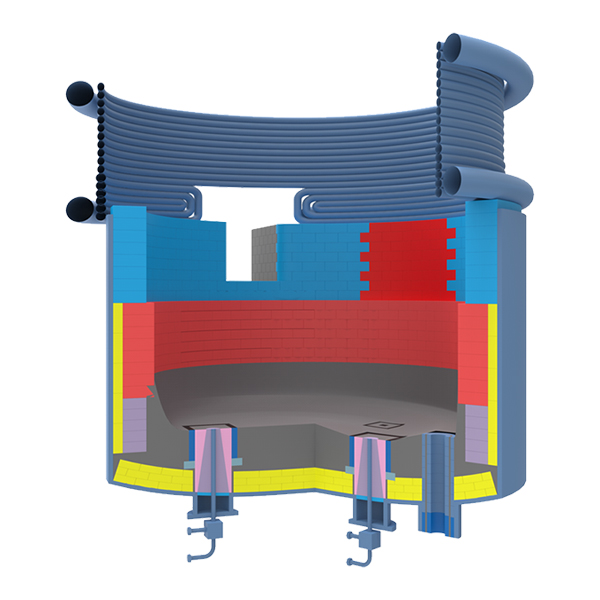
Die allgemeinen Anforderungen an feuerfeste Materialien für Elektrolichtbogenöfen sind:
(1) Die Feuerfestigkeit sollte hoch sein.Die Lichtbogentemperatur übersteigt 4000 °C und die Temperatur bei der Stahlherstellung beträgt 1500 bis 1750 °C, manchmal sogar 2000 °C, sodass feuerfeste Materialien eine hohe Feuerfestigkeit aufweisen müssen.
(2) Die Erweichungstemperatur unter Last sollte hoch sein.Der Elektroofen arbeitet unter Hochtemperaturbelastungsbedingungen und der Ofenkörper muss der Erosion von geschmolzenem Stahl standhalten, daher muss das feuerfeste Material eine hohe Erweichungstemperatur aufweisen.
(3) Die Druckfestigkeit sollte hoch sein.Die Auskleidung des Elektroofens wird durch den Aufprall der Ladung beim Beschicken, den statischen Druck der Stahlschmelze beim Schmelzen, die Erosion des Stahlflusses beim Abstich und mechanische Vibrationen während des Betriebs beeinflusst.Daher muss das feuerfeste Material eine hohe Druckfestigkeit aufweisen.
(4) Die Wärmeleitfähigkeit sollte gering sein.Um den Wärmeverlust des Elektroofens zu verringern und den Stromverbrauch zu senken, muss das feuerfeste Material eine schlechte Wärmeleitfähigkeit aufweisen, d. h. der Wärmeleitfähigkeitskoeffizient sollte klein sein.
(5) Die thermische Stabilität sollte gut sein.Innerhalb weniger Minuten vom Abstich bis zur Beschickung sinkt die Temperatur bei der Stahlerzeugung in Elektroöfen stark von etwa 1600 °C auf unter 900 °C, sodass feuerfeste Materialien eine gute thermische Stabilität aufweisen müssen.
(6) Starke Korrosionsbeständigkeit.Während des Stahlherstellungsprozesses haben Schlacke, Ofengas und geschmolzener Stahl eine starke chemische Erosionswirkung auf feuerfeste Materialien, sodass feuerfeste Materialien eine gute Korrosionsbeständigkeit aufweisen müssen.
Auswahl feuerfester Materialien für Seitenwände
MgO-C-Steine werden üblicherweise zum Bau der Seitenwände von Elektroöfen ohne wassergekühlte Wände verwendet.Die Hot Spots und Schlackenlinien unterliegen den härtesten Betriebsbedingungen.Sie werden nicht nur durch geschmolzenen Stahl und Schlacke stark korrodiert und erodiert sowie durch die Zugabe von Schrott stark mechanisch belastet, sondern sind auch der Wärmestrahlung des Lichtbogens ausgesetzt.Daher werden diese Teile aus MgO-C-Steinen mit hervorragender Leistung hergestellt.
Bei den Seitenwänden von Elektroöfen mit wassergekühlten Wänden erhöht sich durch den Einsatz der Wasserkühlungstechnologie die Wärmebelastung und die Einsatzbedingungen sind strenger.Daher sollten MgO-C-Steine mit guter Schlackenbeständigkeit, Thermoschockstabilität und hoher Wärmeleitfähigkeit ausgewählt werden.Ihr Kohlenstoffgehalt beträgt 10–20 %.
Feuerfeste Materialien für Seitenwände von Ultrahochleistungs-Elektroöfen
Die Seitenwände von Ultrahochleistungs-Elektroöfen (UHP-Öfen) werden größtenteils aus MgO-C-Steinen gebaut, und die Hot Spots und Schlackenlinienbereiche werden aus MgO-C-Steinen mit hervorragender Leistung (z. B. MgO-C mit Vollkohlenstoffmatrix) gebaut Ziegel).Verbessern Sie die Lebensdauer erheblich.
Obwohl die Ofenwandbelastung aufgrund von Verbesserungen bei den Betriebsmethoden von Elektroöfen verringert wurde, ist es für feuerfeste Materialien immer noch schwierig, die Lebensdauer von Hot Spots zu verlängern, wenn sie unter UHP-Ofenschmelzbedingungen betrieben werden.Daher wurde die Wasserkühlungstechnologie entwickelt und angewendet.Bei Elektroöfen mit EBT-Abstich erreicht die Wasserkühlfläche 70 %, wodurch der Einsatz feuerfester Materialien erheblich reduziert wird.Moderne Wasserkühlungstechnologie erfordert MgO-C-Steine mit guter Wärmeleitfähigkeit.Für den Bau der Seitenwände des Elektroofens werden Asphalt, kunstharzgebundene Magnesiasteine und MgO-C-Steine (Kohlenstoffgehalt 5–25 %) verwendet.Unter starken Oxidationsbedingungen werden Antioxidantien hinzugefügt.
Für die durch Redoxreaktionen am stärksten geschädigten Hotspot-Bereiche werden für den Bau MgO-C-Steine mit großkristallinem Schmelzmagnesit als Rohmaterial, einem Kohlenstoffgehalt von mehr als 20 % und einer Vollkohlenstoffmatrix verwendet.
Die neueste Entwicklung von MgO-C-Steinen für UHP-Elektroöfen besteht darin, durch Hochtemperaturbrennen und anschließende Imprägnierung mit Asphalt sogenannte gebrannte, asphaltimprägnierte MgO-C-Steine herzustellen.Wie aus Tabelle 2 ersichtlich ist, steigt im Vergleich zu unimprägnierten Ziegeln der Restkohlenstoffgehalt von gebrannten MgO-C-Steinen nach der Asphaltimprägnierung und Rekarbonisierung um etwa 1 %, die Porosität nimmt um 1 % ab und die Biegefestigkeit und der Druck bei hoher Temperatur nehmen ab Die Festigkeit wurde deutlich verbessert, sodass eine hohe Haltbarkeit gewährleistet ist.
Feuerfeste Magnesiummaterialien für Seitenwände von Elektroöfen
Elektroofenauskleidungen werden in alkalische und saure Auskleidungen unterteilt.Ersteres verwendet alkalische feuerfeste Materialien (wie feuerfeste Materialien aus Magnesia und MgO-CaO) als Ofenauskleidung, während letzteres Quarzsteine, Quarzsand, weißen Schlamm usw. zum Aufbau der Ofenauskleidung verwendet.
Hinweis: Als Ofenauskleidungsmaterialien verwenden alkalische Elektroöfen alkalische feuerfeste Materialien und saure Elektroöfen saure feuerfeste Materialien.
Zeitpunkt der Veröffentlichung: 12. Okt. 2023